In the carpentry factory our apprentices build their future
Marchel used to be a personal trainer, but he changed direction. Meanwhile, Rody was already an all-round carpenter, but he was looking for a specialisation. Both ended up with our colleague and mentor Peter, who teaches them the tricks of the trade in the Ballast Nedam Materieel carpentry factory.
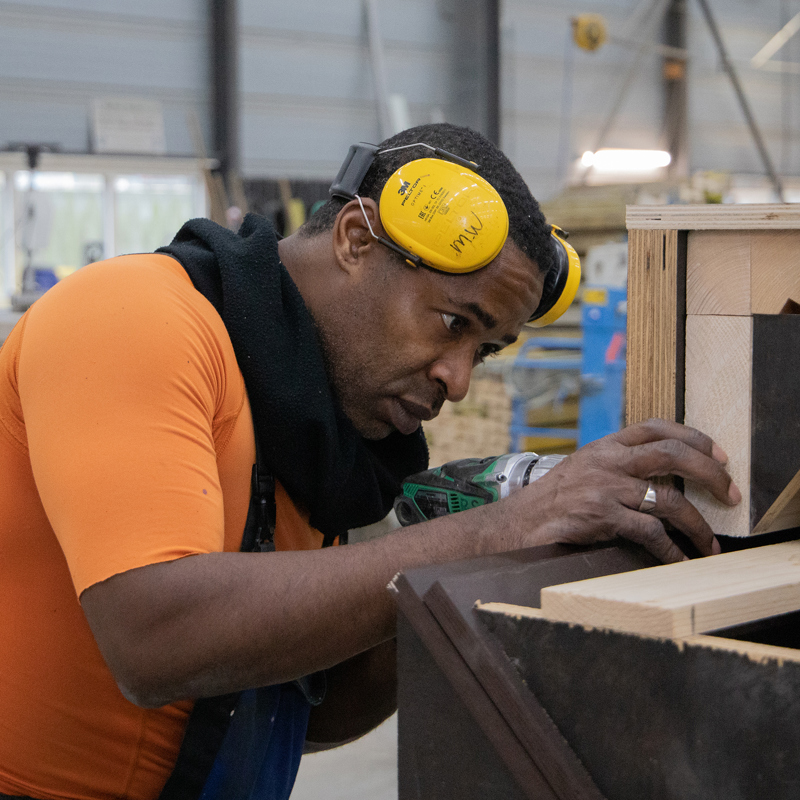
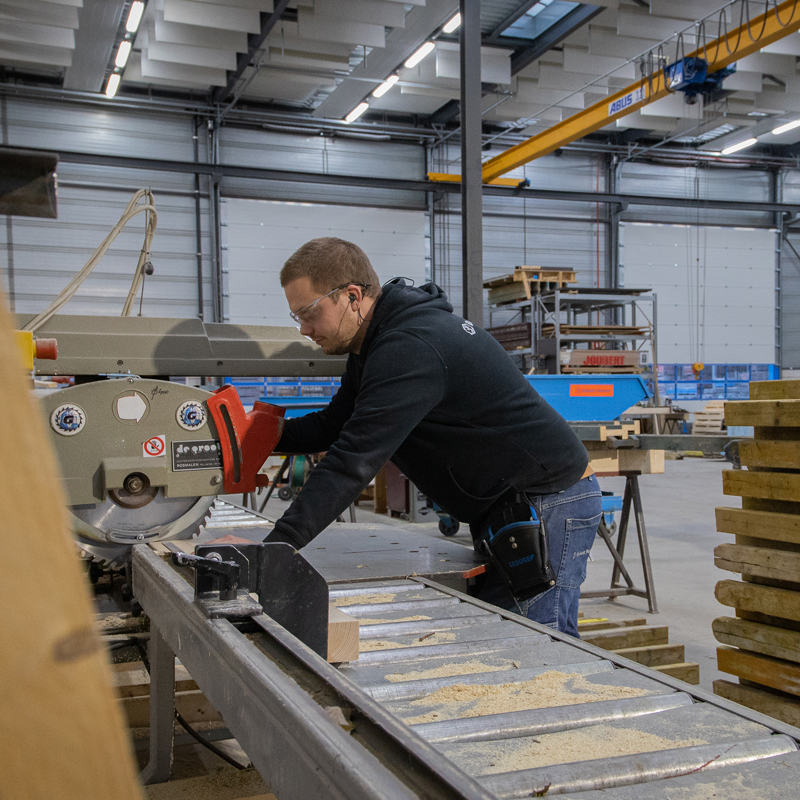
Training to become a concrete carpenter
Marchel and Rody are taking a BBL course to become all-round concrete carpenters and they attend their training course four days a month. There, they learn how to make drawings, read drawings, make calculations and apply relevant environmental legislation to their work. The other days of the week, they work under the supervision of their mentor Peter in Ballast Nedam's carpentry factory. "In the past year I have already learned a lot," says Marchel. "The pieces we make in this factory have to be exactly as shown on the drawing. That is why we work very precisely and it comes down to the millimetre. I surprised myself when I found out that this precision suits me quite well. But I still want to grow in the area of drawing and reading. That's what it comes down to in the end. Meanwhile, his mentor climbs a staircase and takes a drawing from a cupboard on the wall. "That's why you have to practise a lot," says Peter. "Come and have a look at this one. Let's see if you recognise everything."
Education at Ballast Nedam
Two right hands and plenty of enthusiasm are essential ingredients for securing an apprenticeship with Ballast Nedam. Every year, an eager group of apprentices start working at Ballast Nedam. They are trained as, for example, Machinists, Drill Supervisors, Pile-drivers or Carpenters.
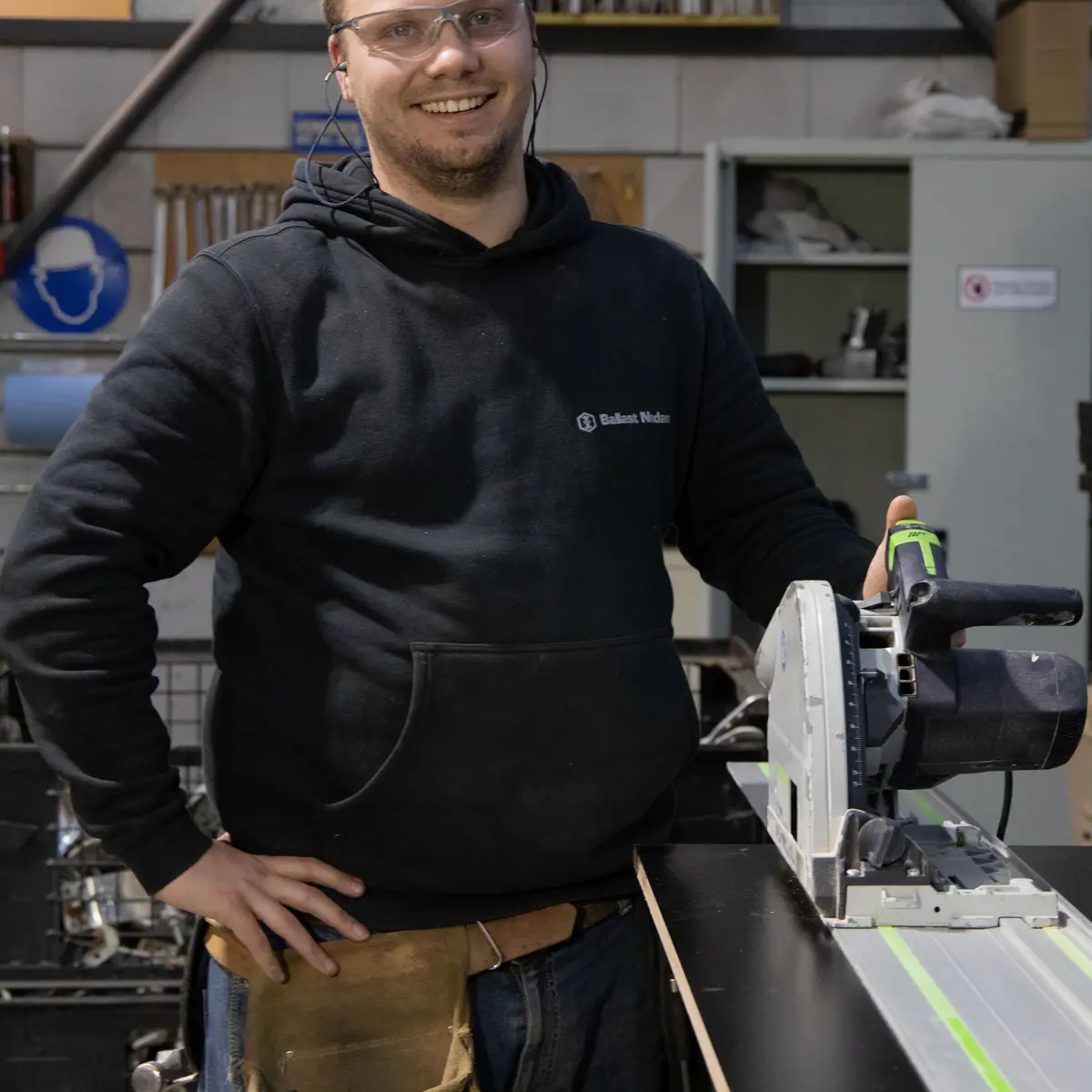
'How could this have been made?'
Before Rody started working in the carpentry factory, he did not know the concept of 'concrete carpentry' and when he drove under a bridge, he did not notice the pillars or other elements of the construction. But that has changed now. "I now routinely ask myself: how would this have been made? The pieces we make are later fully incorporated into the whole. But I now know how much work is hidden there. For example, I made the walls for the A9 Gaasperdammertunnel. They are 13 by 5 metres, or sometimes even bigger. You can imagine that they involved a lot of screws and clamps. They were transported by night from our factory in Almere to Amsterdam. That makes me really proud."
Tip: Here you can find all the internships and apprenticeships at Ballast Nedam