Tunnel technical installations: how does it work?
Without you realising it during your trip through a tunnel, dozens of systems continuously monitor the safety of you and other road users. For example, they intervene at high speed when a car catches fire. These systems are called 'tunnel technical installations'. This is an expertise Ballast Nedam which is constantly expanding.
Meanwhile, the tunnel is being shut down. Traffic is slowed down, traffic lights turn red and the barriers are lowered. Road users in the tunnel can escape via the escape doors, where they are guided in the right direction. Meanwhile, the road traffic controller can call emergency services and instruct road users via the public address system. All these steps happen at lightning speed. Because time is ticking.
Ballast Nedam is carrying out this expertise within, among other things, project A24 Blankenburgverbinding in Vlaardingen and Rozenburg, commissioned by the Directorate-General for Public Works and Water Management (Rijkswaterstaat). In this project we are designing, realising and maintaining the technical installations for the Hollandtunnel, Maasdeltatunnel and on the A24, A15 and A20 national highways. In Limburg, Ballast Nedam is also renovating the Roertunnel and Tunnel Swalmen (A73) for Rijkswaterstaat, together with Croonwolter&dros. This involves replacing the existing tunnel technical installations.
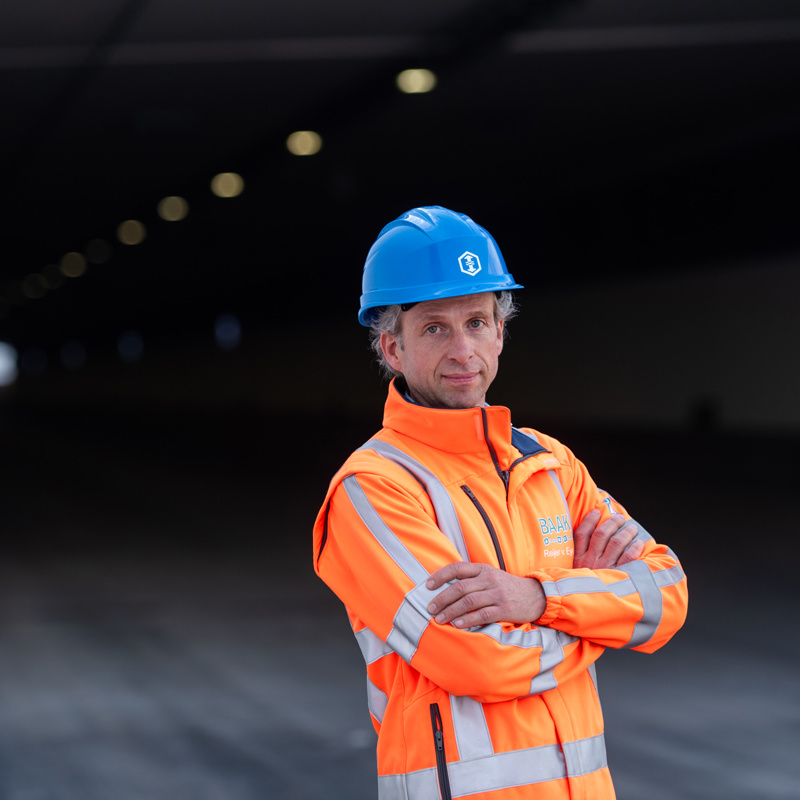
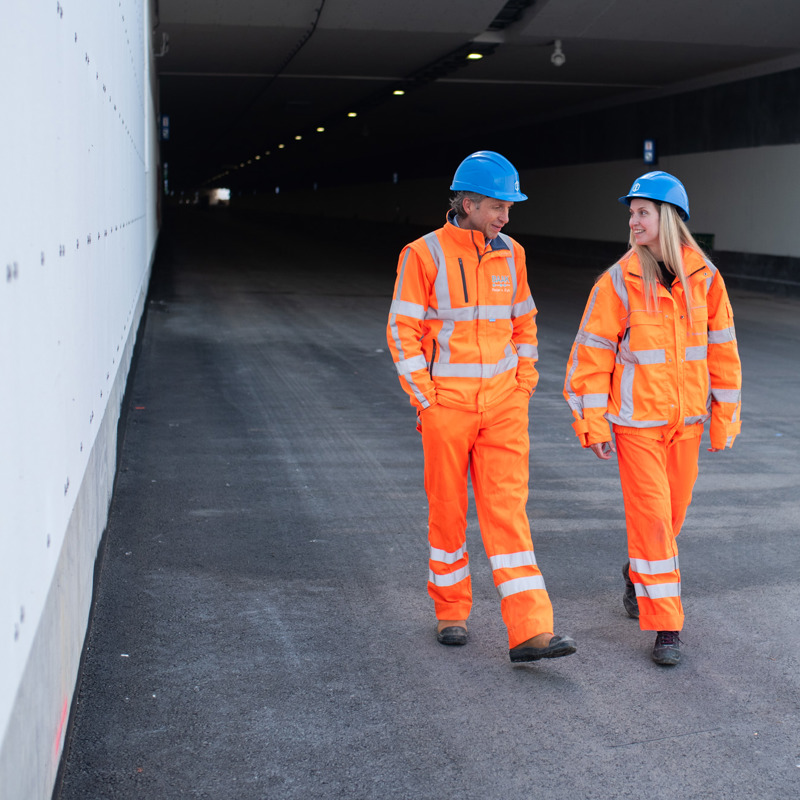
Reijer, why are these systems so important?
"The main objective is clear: to create safety. The installations help prevent incidents and accidents. When an accident does occur, the systems manage its impact. Through smoke control, for example. In addition, the systems promote the self-reliance of road users thanks to escape route indication and facilitate emergency assistance."
What exactly did we do on tunnel technical installations for the Holland Tunnel?
"The Holland Tunnel is over 500 metres long and has many systems, all under our responsibility. But it actually starts outside. Before entering the tunnel, you see the movable guide rail in the central reservation, the barriers, traffic lights, speakers, cameras, light fittings and fans. In addition, the tunnel has facilities for public address, intercom, camera surveillance, lighting, emergency boxes, a secure escape and service corridor, overpressurisation system against the ingress of smoke, cellars and pumping systems for liquid drainage and a fire extinguishing facility. Actually, it is too much to mention. In the service buildings, there are technical rooms for power supply, transmission and building installations. The whole package is here."
And what about the Maasdeltatunnel, which is a bit further down the road?
"The Hollandtunnel is a land tunnel and the Maasdeltatunnel is an immersed tunnel under the river Scheur, but in terms of tunnel-technical installations, it's basically the same. However, the central heart of all tunnel technical installations is in the southern service building of the Maasdeltatunnel. All central control boxes of the installations of both tunnels are located there, as is the local operating desk. In theory, the tunnels are operated from Verkeerscentrale Rhoon, but as a back-up, this can also be done locally from this service building.
Also nice to mention: besides designing, purchasing, realising, commissioning, integrating and testing, we have developed a fully-fledged education and training system. This has now been installed at the traffic control centre in Rhoon, so that the future traffic controllers of the Hollandtunnel and Maasdeltatunnel will be able to operate it properly after opening."
During this work, what is the challenge?
"We are focusing on making this project predictable. My work often has a reputation revolving around 'hassle'. Tunnels that can't open because integration and tests go off, things like that. My challenge and ambition on this project is to squash that. That is why we have a tight integration and testing process here, with an advanced and fully integrated test environment. In that test environment, all systems are tested 1-to-1. We go much further here than on our previous tunnel projects."
Tell us, how does that work?
"You have to think of it as a three-stage rocket. The first step is that the complex and high-risk components of the tunnel systems are already fully built and integrated in our test environment. Thus, everything is pre-tested: the software, the interfaces between system components, and all central control systems including the complete tunnel configurations and other critical parts of the systems. In doing so, we used the final operating desk, and where appropriate, as many of the same tunnel technical system components as those used in the tunnels. That setup is representative of how the tunnel will work later. That goes even further than a simulator."
As a second step, we test all systems again when they are actually installed in the Holland Tunnel. We check the installation and commissioning, looking in particular at operation and physical dynamic behaviour. How is the installation and commissioning process going with our partners? How are the audio and camera surveillance working in the production environment? How are the air velocities in the traffic tube? Is the overpressure working? These are things we learn a lot from.
Finally, we apply the lessons learned from the test environment and Holland Tunnel in the Maasdeltatunnel. So we have actually had two dress rehearsals for that. We need that certainty as we are dealing with a tight schedule. This way, we minimise our lead time and can do our work much more reliably."
In the Hollandtunnel, all systems are now being put into operation, how is that going?
"That's right. All systems are thoroughly tested after assembly, integration and commissioning. This is done on the basis of all test cases and scenarios that were thought out beforehand. For example, we found out that the final image quality of the camera surveillance system and cameras shown on the operator desk was not at the level we had expected beforehand after all. So during the testing phase of the Holland Tunnel, we were able to investigate and fine-tune this.
What is special is that we are currently commissioning and testing the Hollandtunnel installations by means of a network rerouting via the Thomassentunnel and the Maeslantkering. We do this because the Maasdeltatunnel will not be completed until later and, as a matter of course, we cannot yet establish a connection between the central equipment of the Maasdeltatunnel and the Hollandtunnel installations."
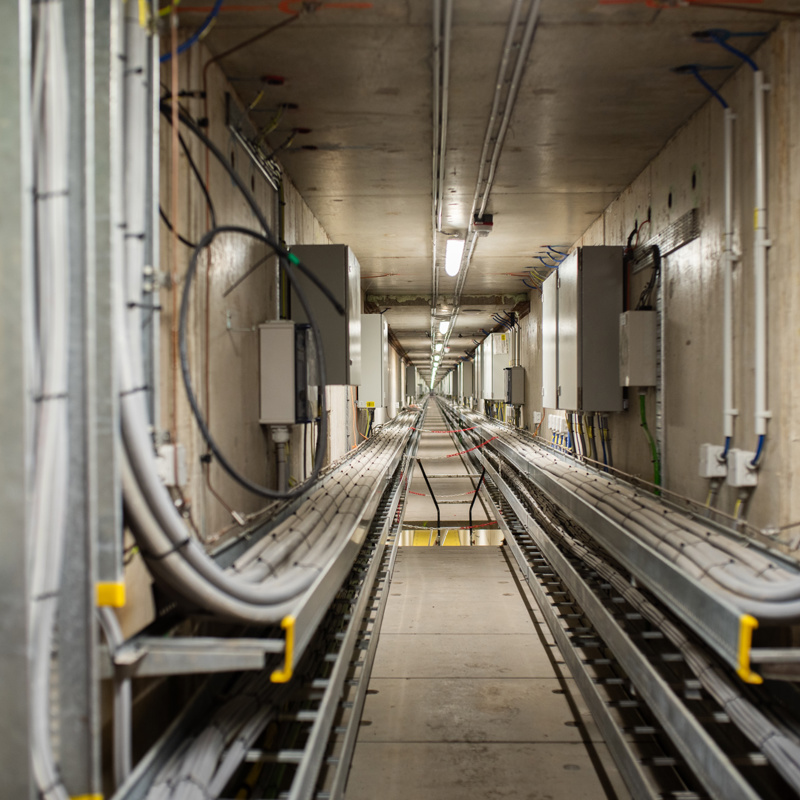
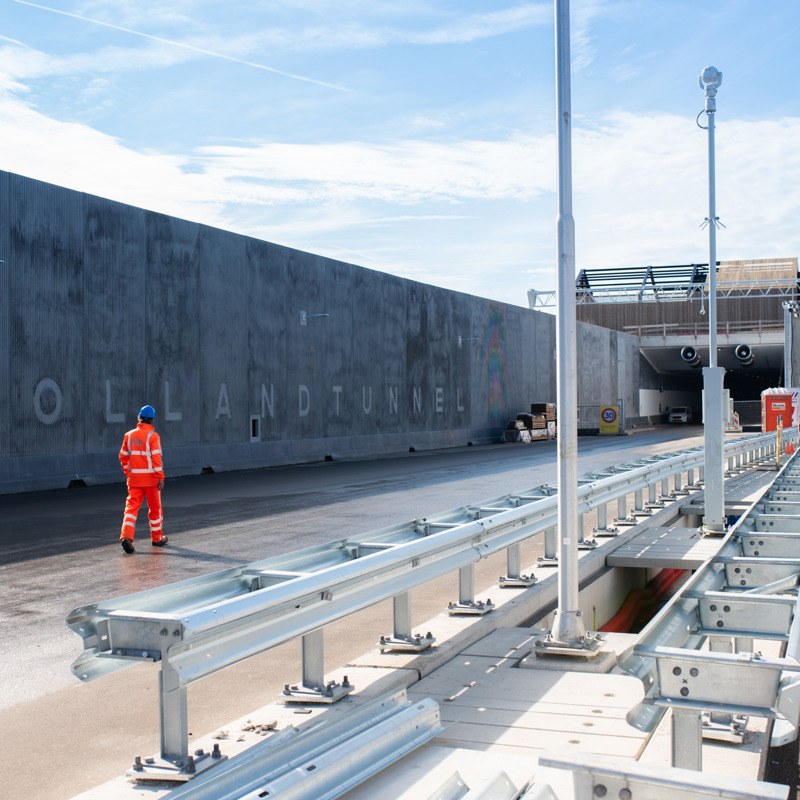
Is this expertise becoming increasingly important within Dutch infrastructure?
"Basically, it has always been important to ensure safety in tunnels. We see that we are keeping up with the innovations in the market in this area, with systems becoming smarter and more advanced. Moreover, in the Netherlands we are facing a huge job of renewing and renovating our tunnels. So within that task, many installations also need to be replaced. Ballast Nedam is fully committed to this and we are even expanding our teams of specialists for this.
For example, we are already renewing and renovating tunnel technical installations in the Roertunnel and Tunnel Swalmen (A73), together with our consortium partner Croonwolter&dros. These works will be fully completed by 2024, allowing road users to drive through these tunnels in accordance with the highest safety requirements as well. That feels good!"