Industrial modular construction: one solution for multiple problems
Heddes Bouw & Ontwikkeling, a Ballast Nedam business unit, is working with Ursem Modulaire Bouwsystemen* and Schouten Techniek on industrially produced, modular homes. One project involves 300 student houses in Amsterdam, the other 44 spacious flats for social housing tenants in Schagen. For the latter project, commissioned by housing corporation Wooncompagnie, the entire complex 'De Tramhalte' was assembled on site within three weeks in November 2023.
But there are more advantages. Building in the factory means building in optimal conditions. You won't be bothered by wind and rain. That makes it easy to ensure the quality of the work. And once the modules go to site, a complete building is erected there within a few weeks. Different from the many months, or sometimes even longer, involved in traditional construction. “So there is much less inconvenience on site for a much shorter time”, Boaz says. “Both in terms of noise and construction traffic and emissions. The latter also means a big plus in terms of the nitrogen issue.” Another advantage: industrial housing construction bypasses the scarcity of technical professionals. Unlike the traditional construction site, the assembly line at Ursem's factory does not require all-round carpenters, but employees who can perform certain tasks well. “The pool of personnel we fish in is therefore quite large,” he says.
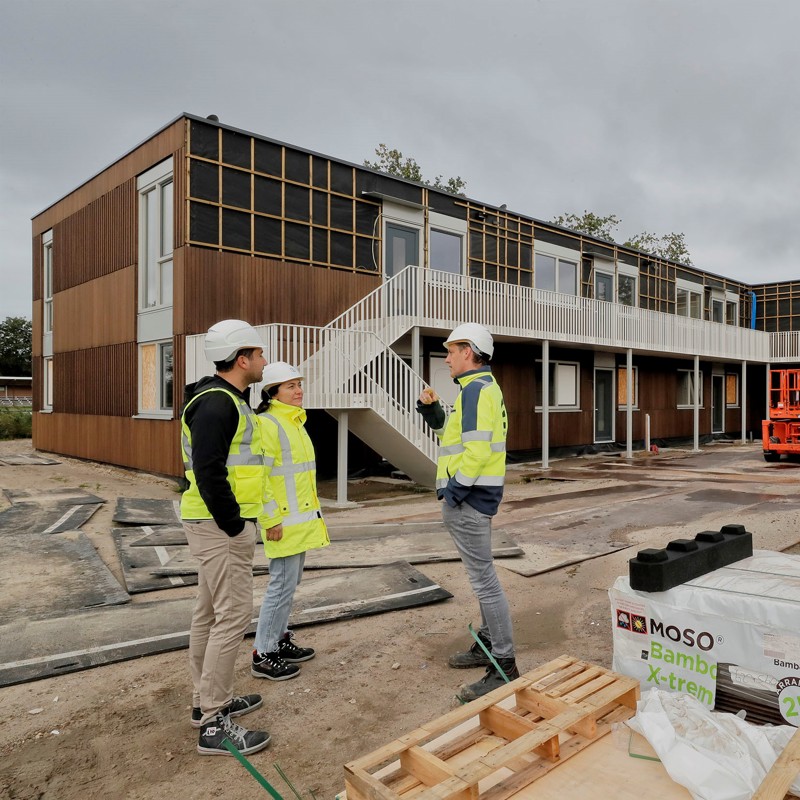
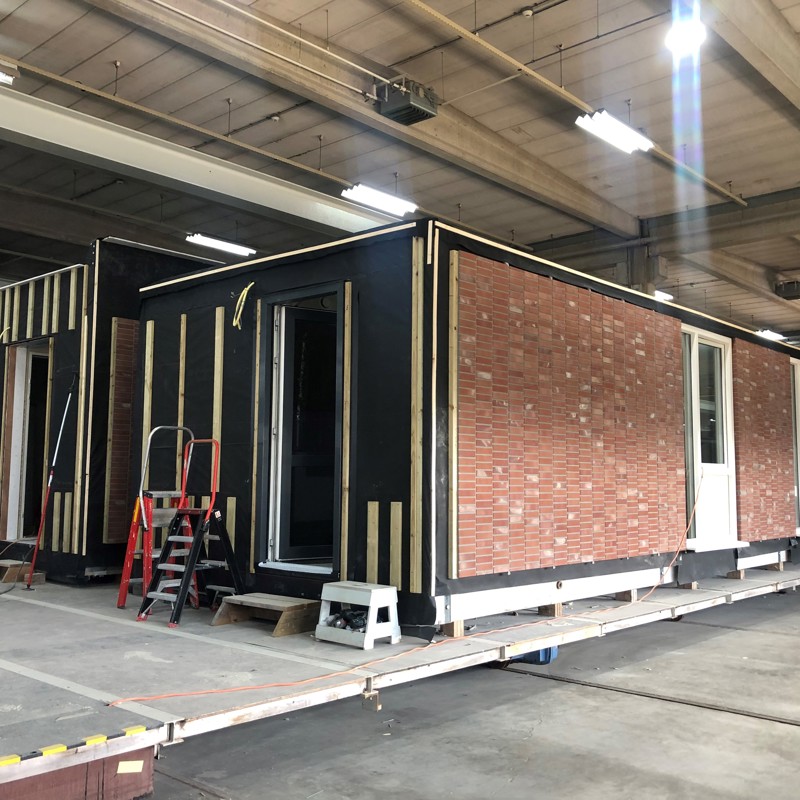
Singles and small families
Project developer Peter Cornielje of Wooncompagnie: “Regioplein was our first project with modular homes. The experiences were positive, both from us as clients and from the residents. That encouraged us to try for more. So for De Tramhalte, I put the main outlines on paper based on Regioplein itself, including the modules we wanted. Then I took my drawings to Heddes and asked: can you make this?” The answer was in the affirmative. Peter is a strong advocate of conceptual, industrial and modular construction. He largely concurs with the aforementioned benefits. “We are depleting the earth. That is why it is important to use bio-based materials, and also bet on circularity through detachability and movability of all the elements that make up the building.” This, Peter knows, makes projects eligible for the Environmental Investment Allowance (MIA). This was also successful at De Tramhalte. “Heddes went to great lengths to achieve this, using bio-based materials and FSC wood, plus providing all the documentation required for the MIA.”
Increasingly sustainable
The Netherlands needs more than 100,000 houses a year, but that number is not being met for now due to many delaying factors, rising costs and the aforementioned nitrogen issue. Does industrial, modular building represent the solution to tackling many of these problems? “You cannot say it is the solution. But because of the speed of production and low emissions, we do form part of the solution to the housing shortage.” For Boaz personally, in turn, it feels good to be part of it. “We are also able to make exclusive housing, but the bulk of it is social sector housing anyway. So we build those for people who don't have unlimited resources, but still want a roof over their heads. I like the fact that we can help meet that need.”
Thinking together
“You really do it together. And even though you buy an existing product, they are willing to think along with you. For instance, the balcony doors originally opened inward. We preferred not to do that. Because the turning radius then takes away space inside. Besides, when it rains it means that water drips onto the floor of the house as soon as you open that door. We know from experience that tenants will complain about that. I know that in a case like this, other system builders say: there's no other way, because it won't fit into our system. But after some pleasant haggling, Heddes, Ursem and Schouten modified their system for us. The balcony doors now open outward.”
Structural position
So industrial and modular construction seems to be moving forward. Also because a key hurdle, the approval of Building Regulations Committees, is getting better and better. “In permit applications, the Building Inspectorate was particularly critical of the visual quality of modular houses,” says Boaz. “But they are now taking an increasingly constructive stance. This is partly because we are paying more and more attention to it. For instance, we work a lot with the renowned firm Uytenhaak + partners architects. That way, you form a good discussion partner for Welstand, and you show that you also take the aesthetic aspect of modular housing seriously. In this way, we arrive at an increasingly beautiful, better, more sustainable and affordable product along several paths.”
The Building Quality Assurance Act
De Tramhalte was a pilot project for Heddes under the Building Quality Assurance Act (Wkb). Heddes gained experience with the VKB quality assurance instrument during this pilot together with quality assurance company PlanGarant. This involved using Dalux Field for quality checks and Dalux Box for document management. The result are various learning experiences that Heddes will use to comply with the law in future Wkb projects in a way that fits in with practice, is efficient and user-friendly.
Heddes was the first company within Ballast Nedam to receive the "declaration of justified trust" from PlanGarant. With this, PlanGarant has indicated that, in its opinion, there is justified confidence that the project complies with the rules of the Buildings Decree.
* Ballast Nedam has a 50% stake in Ursem Modulaire Bouwsystemen.