Velsertunnel
Between 1952 and 1957 the Velsertunnel was built under the North Sea Canal. It was considered a monument of modernisation in the Dutch contracting industry. For the Amsterdamsche Ballast Maatschappij (ABM) the tunnel was the largest work in its then almost 80-year existence.
-
1644 metres length of motor tunnel
-
3224 metres length railway tunnel
-
10 thousand tonnes steel sheet piling
A project full of innovations
The Velsertunnel was built in a dry construction pit. It was an innovation to use this time-honoured method for shallow tunnels in a 24-metre-deep pit with high slopes and a large reduction in the groundwater level. Also new was the large-scale cooperation of experts, companies and the Directorate-General for Public Works and Water Management, which had been contracted by a single contractor in a single project. This made possible an integral approach that brought about notable innovations, time savings and labour savings.
Three-part construction
The Velsertunnel was built in three parts, without interrupting shipping traffic on the busy North Sea Canal. This was possible because the canal had to be widened at the same time. On the bank of the site intended for widening, a round construction pit was dug from sheet piling. The middle section of the tunnels was constructed in this pit. From there, a construction pit was dug in which the southern tunnel section was built. The Noordzeekanaal was then shifted above this section of the tunnel, with a cofferdam as temporary bank, and the building pit for the northern section of the tunnel could be made.
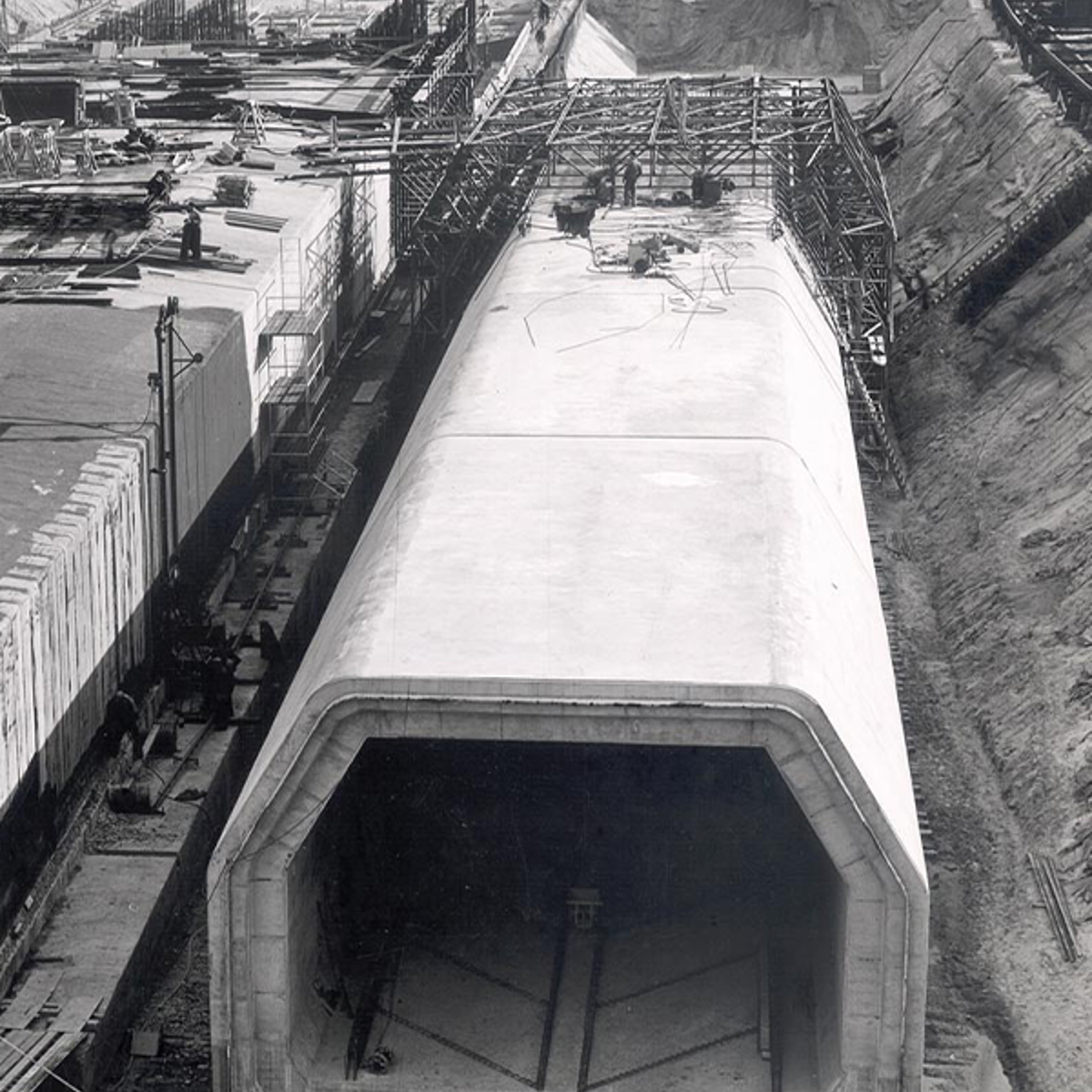
Mechanisation
The ABM fully exploited the opportunities for mechanisation available at the time. For the first time, tower cranes could be seen on a hydraulic construction site. Sand, gravel and cement were delivered by ship to two concrete batching plants, from where the concrete was transported by high tippers and brought into the work via a pump or conveyor belt. A new approach that proved very efficient. Also new was the use of mobile steel formwork for the construction of the total of 270 tunnel elements. This yielded considerable time savings: the eighteen-metre-long elements were produced in three (railway tunnel) to four (road tunnel) weeks.
Concrete assembly building
Precast concrete also saved a great deal of time. When manpower and time were lacking to make the concrete light grids for the entrances, this could be solved with pre-stressed precast slabs that were placed by cranes. In addition, the construction of the concrete substructure of the eight northern ventilation towers threatened to take too long. The reason for this was the unusual shape and the many recesses. A solution was found in the construction of the substructure in prefabricated concrete 'discs'. These were constructed in just twenty days, saving more than three months' time. This method was called 'Operation Pineapple'. The operation was more expensive in direct costs, but the time saved yielded a higher value in cost savings. History was written with this operation: in the next two decades, the ABM made a name for itself with concrete assembly in large utility and infrastructure projects.