Construction of tunnel for new land route
Faster, more direct and safer transport from the Far and Middle East to Europe. That's the vision behind Iraq's Grand Faw Master Plan, also known as the New Silk Road. As part of this extensive infrastructure project, Ballast Nedam is installing 10 tunnel elements in a side-branche of the Euphrates River.
-
10 tunnel sections
-
125 meters length per section
-
46,000 tons per section
Important link
The largest port in the Middle East, that's what Al Faw Port is set to become in the coming years. To open up this growing area to the north, a completely new road is under construction. From Al Faw Port, in the southernmost tip of Iraq, road traffic will soon cross the Khor Al Zubair River via a tunnel. The route then leads through Baghdad to Turkey. This tunnel thus forms an important link in connecting the region with Europe. What this will bring, besides increased trade? Time savings as well as less risk - the new route is intended to be a competitive alternative to the Suez Canal. Currently the advantage is even greater: due to the unsafe situation around the Suez Canal, many ships are now detouring via the Cape.
Floating and warping
10 precast concrete tunnel elements are lined up neatly in the construction dock at the project site. Ready to be immersed, says Martijn Smitt, Executive Director of Ballast Nedam. “Our work involves the following: once the construction dock is flooded, we float the tunnel elements one by one. Then we warp them out of the dock and place them in position using immersion techniques. We also provide a foundation for the tunnel elements to rest on: for this, we create sand pancakes between the bottom of the tunnel element and the riverbed by sandflowing.”
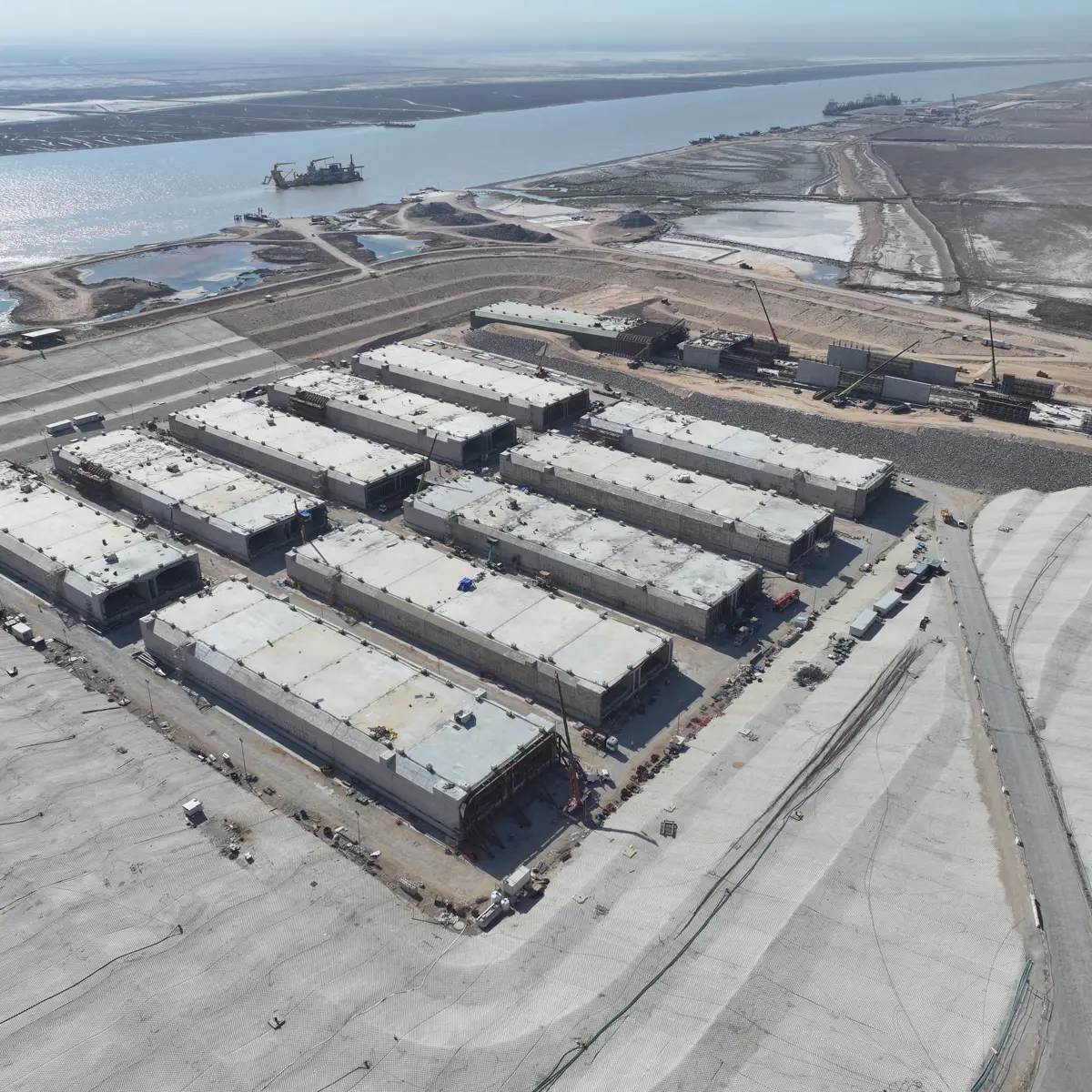
Immersing and connecting
Once the immersion process begins, the tunnel elements are warped out of the dock using winches and temporarily moored at another location. There, we prepare the tunnel element for immersion. We install temporary support structures, bollards and lifting lugs as well as an access shaft, a survey tower and survey systems. Once the large catamaran pontoons are also attached, the immersion can commence.
Using a winch system, we slowly and precisely move the tunnel element to the immersion location: here, winch pontoons hold the tunnel element in the correct position to then carefully and gradually lower it to the riverbed, one tunnel element at a time. The tunnel elements land in a dredged trench and rest at the front (primary side) on a steel support structure and at the rear (secondary side) on a temporary foundation of two massive tiles.
Using hydraulic jacking systems, we can position the tunnel element at exactly the right height. Once on the bottom, the tunnel element is connected to the previous section in a watertight manner using the GINA gasket. An extremely precise and time-consuming job: each immersion operation takes approximately 16 continuous hours. Once the position of the tunnel element is approved, the sandflowing of the tunnel element begins and a pattern of sand pancakes forms the final foundation.
Working in the desert
A highly specialized project, but the location also brings its own challenges. Martijn: “Umm Qasr, just south of Basrah and the exact location of the tunnel, is situated in the middle of the desert. The thermometer regularly hits 50 degrees Celsius. You must continuously protect yourself against this extreme heat to prevent burns and dehydration.”
Besides the climate, political and social unrest also increase the risk. “Working in an area classified as ‘red’ by the Ministry of Foreign Affairs means a great responsibility to ensure safety. We take this very seriously as a company and organize ourselves accordingly. This means we take extensive measures to ensure our people can work safely. For instance, all transport to and from the project site is conducted with armored vehicles and under escort, and the sites are guarded 24/7. The compound is our home base: this is where our people work, eat, sleep, and exercise. Leaving the camp without permission is absolutely forbidden, and strict rules apply. It takes some getting used to. But it is also a unique experience, one that colleagues consciously choose. Working on such a project in which literally failure is not an option and everything has to be right - you only do that a few times in your life.”
Team effort
It certainly is a unique experience. Xavier Szadkowski, Project Engineer at Ballast Nedam, agrees. “I love working abroad. But a location like Iraq is extra challenging; you have to be able to handle that. You don’t make that decision just for yourself; you also want your family to support you. All in all, we spend about a year on the compound. That only works if you are open and willing to contribute to such a special project.”
What helps enormously is good team dynamics, says Xavier. “At first, you don’t know each other: as a group, you have to go through a process before everyone is on the same page. This also applies to the people we work with, the client, and our partners. In the meantime, we have become a group of people who enjoy the work and are eager to create something great together. Together we have to fix it. We are all engineers but in execution we all do it together.”
The technology is the least of our worries, Xavier explains. Getting everything in the right place is the biggest challenge. “Locally we can’t arrange anything; all the equipment comes from other countries. This requires extremely good preparation. We have to think through, check, and double-check every component in detail beforehand. Once the tunnel is there, we can all be immensely proud!”
Investing in development
Ballast Nedam is executing the Umm Qasr project on behalf of its client and main contractor, Daewoo Engineering & Construction Co. A successful implementation of the tunnel connection will contribute to increased transport safety and the economic development of the region. To support these ambitions, the World Bank Group is investing in the Grand Faw Masterplan.
More information?
Martijn Smitt
Executive Director Ballast Nedam
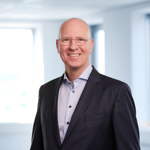