3 of the most interesting developments in the asphalt laboratory in Leerdam
The asphalt on roads and cycle paths has been the subject of much thought for months. Can it be more durable? More stable? More flexible? Thinking up and developing asphalt mixtures is everyday business in Leerdam. There, the laboratory of DIBEC Material Science, part of Ballast Nedam, celebrated its first anniversary. Time for a look back at the three best developments of this first year.
"I have been making mixtures for days. This results in test pieces, which I test for density and strength. We are constantly weighing up the pros and cons: What do we add to bind them together? Will that stay within the client's budget? And how can a mixture be even better for the environment?"
Asphalt mixtures: that's tailor-made
Although the laboratory in Leerdam has only been in existence for a year, it has already gained more than 15 years of experience at its old location. This is vital, because the development of new asphalt takes months. It is a clever piece of physical and chemical research, in which the conditions and environmental factors are always project-specific. That is why it is tailor-made. For every client and every project.
At their new location in Leerdam, the materials technologists work under the same roof as the Ballast Nedam Road Specialties engineers. Ideal, it seems. The low threshold for joining forces means that new ideas can be developed quickly. These can then be developed and tested in the lab. In this way, new mixtures are created for public and private sectors.
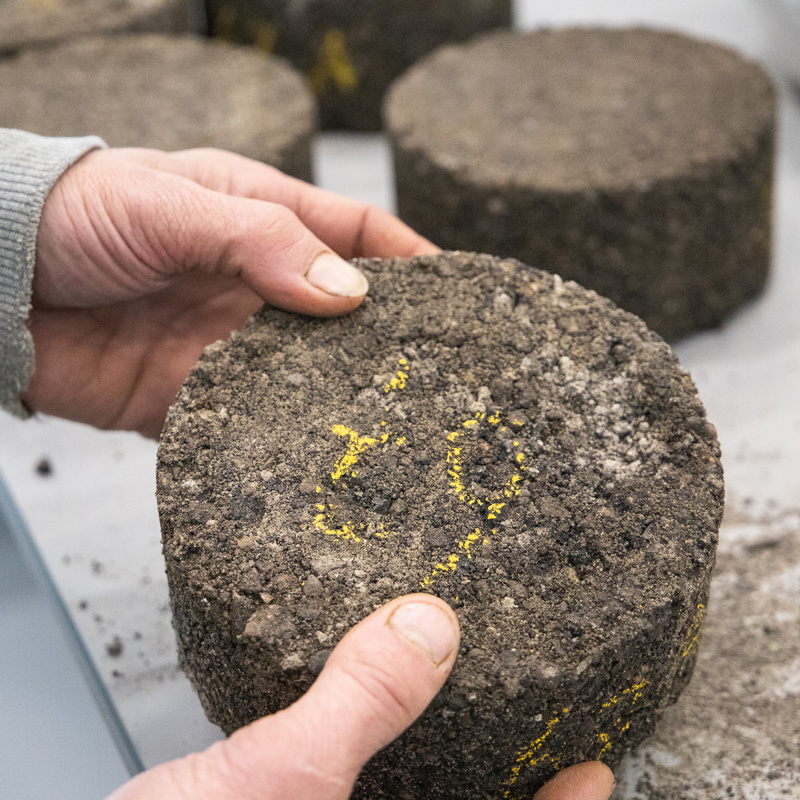
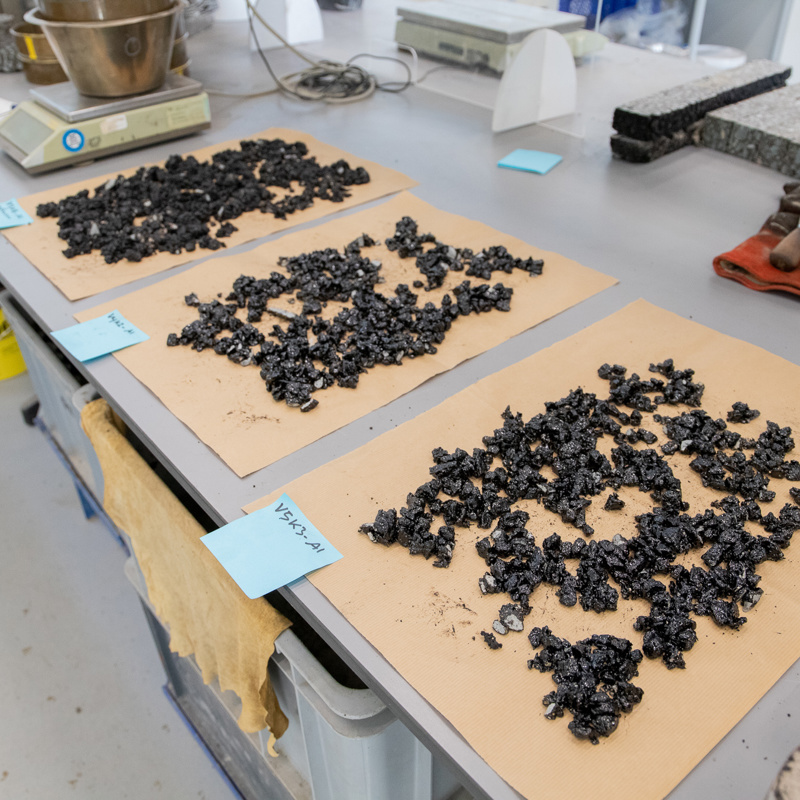
New sustainable developments
The asphalt mixtures that leave this laboratory range from flexible to very stable. Almost all of them have one important factor: CO2 reduction. That is why the mixtures contain as few primary building materials as possible and as many recycled materials as possible.
"There are a lot of sustainable developments in this field," says Jan van de Water. As Head of Materials Science, he has already seen dozens of mixtures leave the laboratory. "Renovating a road or laying new cycle paths can often be much more sustainable than our clients initially think. That is why it is our job to bring these options and opportunities to their attention. That's great: thinking along and surprising them."
3x the best developments
In the past year, DIBEC has produced three sustainable asphalt mixtures that have now found their way into the Dutch road network. In a row:
1. Castricum: New asphalt in close cooperation with the municipality
During a redesign project in Castricum, DIBEC developed a new red asphalt mixture that scores highly in the field of sustainability. The new mixture contains a lot of recycled building materials. Thanks to an improved and clever design, we were able to reduce CO2 emissions by more than 50% compared to the original design.
Jan recalls: "This project fell within Ballast Nedam Road Specialties' framework agreement. At an early stage, we indicated to the municipality that this project offered opportunities, opportunities in terms of sustainability. That's why the client and the contractor were able to transform this project into a sustainability reconstruction."
2. Rijswijk: extensive reuse
An SMA with 65% PR. That code language refers to the mixture that was used in Rijswijk. SMA stands for Stone Mastic Asphalt: a type of asphalt that is used on roads as a covering layer. For a project in Rijswijk, a new mixture for this top layer was developed in the laboratory. The mixture consists of 65% recycled asphalt: a remarkably high score.
The recycled building materials came from the asphalt recycling bank of Ballast Nedam Road Specialties in Amsterdam. Here, Ballast Nedam collects milled old asphalt, which is then processed into new building materials. It is then applied to renovated roads, such as in Rijswijk.
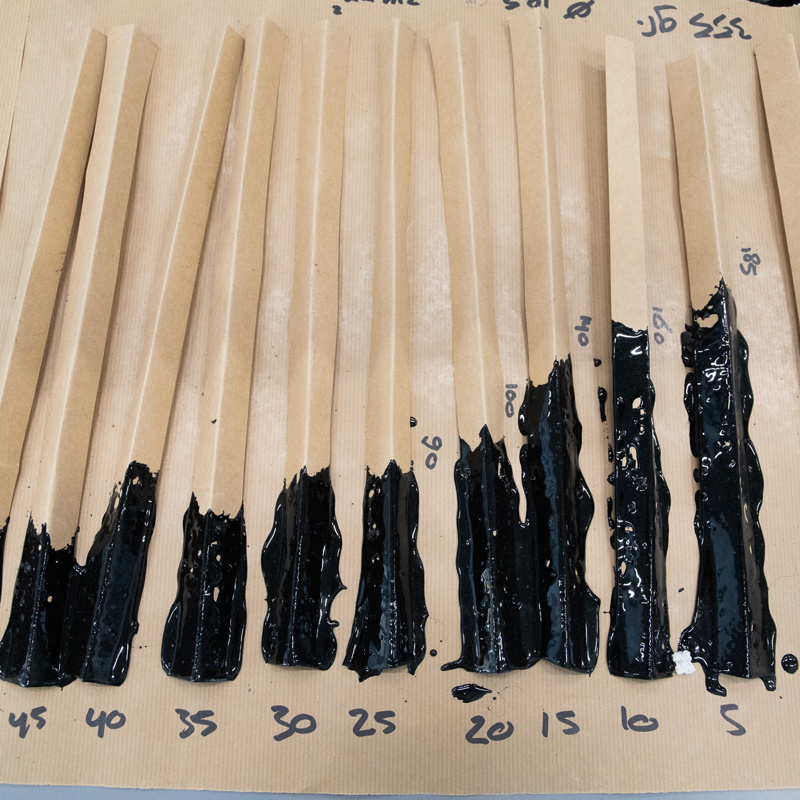
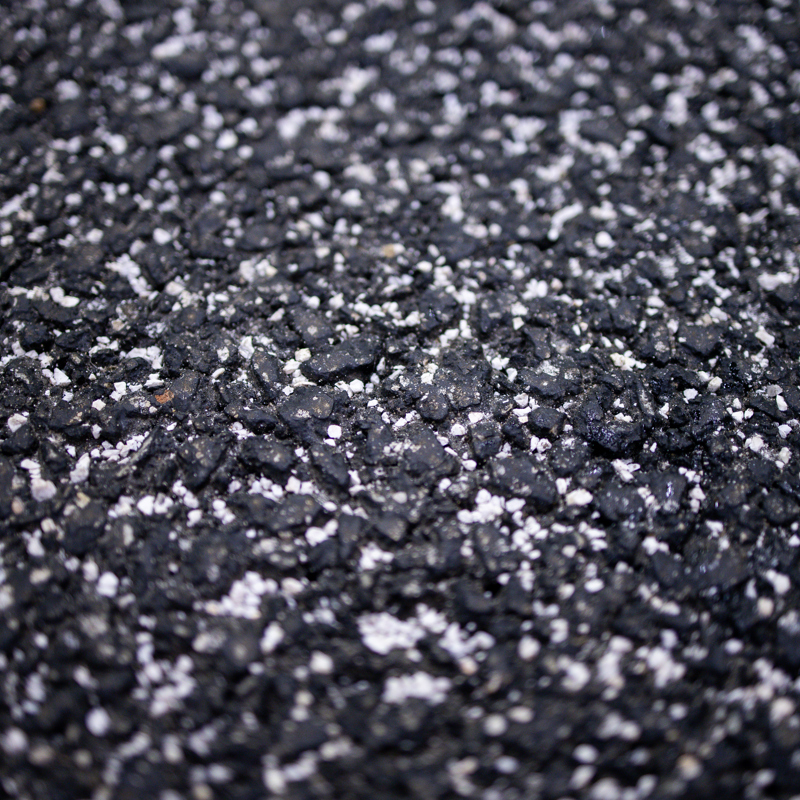
You can hardly see them from a distance, but they are definitely there: small white stones in the grey asphalt. This so-called 'white crushed stone' has many advantages. The stones reflect the light of street lamps and headlights. This gives road users better visibility and public lighting can shine a little less brightly. Benefits? Safety, energy savings and a contribution to reducing global warming.
"In this development for the municipality of Dordrecht, we applied our knowledge from the A9 Gaasperdammerweg project, among others," says Jan. "There, we also used white crushed stone in the mixture for the Gaasperdammer Tunnel. This provided better visibility on the road and it saved energy in the tunnel because the stones reflect the light. In addition, the asphalt becomes less hot in summer and the surface therefore remains in better condition. Not an unnecessary detail, with the current climate.
More than satisfied in Leerdam
The Leerdam site has proved to be a permanent fixture over the past year. Jan's team is once again hard at work on new mixtures for new or renovated roads. "Cliché but true: the glass is always half full here. That is due to the creativity of the group. They come up with ten solutions for every challenge and I come up with the eleventh. That's how it works."