Renewal Noordeindseweg Delft
Large in innovation and complexity, small in size: that is the Noordeindseweg project in Delft. Ballast Nedam has replaced 800 metres of asphalt in a circular and sustainable manner. We have worked in a construction team with the municipality of Delft.
-
800 metres asphalt
-
90 per cent reuse
-
1 construction team bouwteam
Foam bitumen as a solution
The old Noordeindseweg had suffered many cracks and irregularities because of the sensitive peat soil. Foam bitumen stabilisation therefore offered a solution: we mixed the old asphalt road and added foam bitumen and the durable cement to the milling material. This solution can move more easily with deformations, without causing the construction layer to crack. Ideal for road constructions on peat substrates. This is how we achieved a flexible, sustainable and load-bearing foundation.
Cooperation with TNO
Can we use geopolymer cement as a sustainable cement substitute in foam stabilisation? The research organisation TNO has investigated this question. From their literature research, they concluded that geopolymer cement is not yet suitable for an in-situ dry application and therefore the choice fell on the white, sustainable cement product Eco2cem.
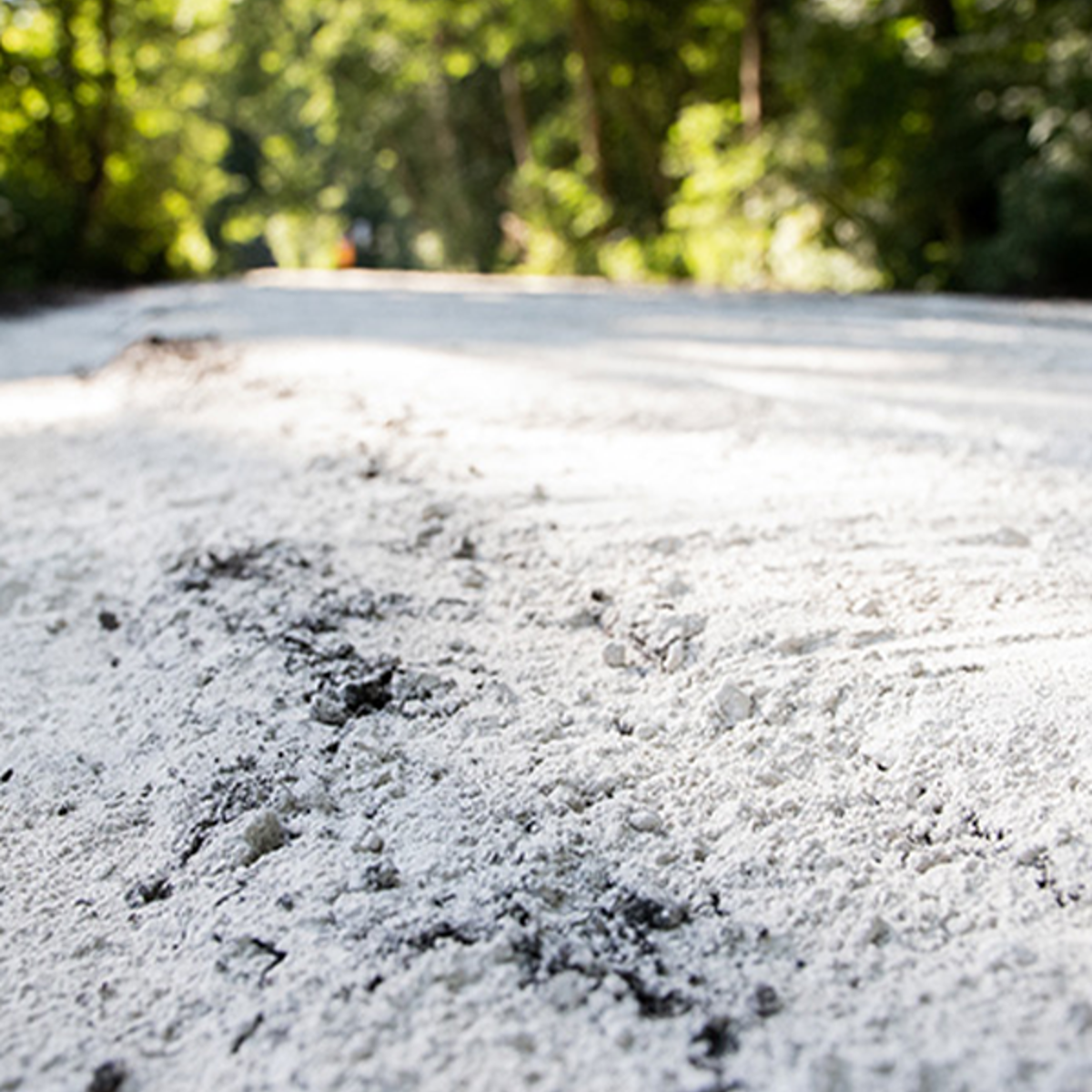
Test pieces and mixtures
On the Noordeindseweg, we reused as many construction materials as possible. But: how does the most suitable mixture come about? In the laboratory of DIBEC Materiaalkunde we composed 5 possible mixtures that differ in the amount of bitumen to be added and different types of cement. After making and examining the samples, the most suitable mixture emerged: 60% asphalt granulate and 40% slag granulate, plus 2.5% bitumen and 1% ground granulated blast furnace slag: the sustainable cement Eco2cem proposed by TNO. This chosen asphalt mixture met the required paving properties and provided the maximum EIP reduction compared to the standard mixture.
Testing, testing, testing
With data and technology, we ensured that the renewed road has the highest possible quality. Drill core investigations showed that the existing bonded slag foundation contained a steel reinforcement, after which we used radar measurements to determine at what depth this reinforcement lies. We processed this data into a detailed map to prevent damage to the chisels during milling.
A truly sustainable solution
Our sustainable solutions go beyond circularity. We carried out some of the road works using electrical equipment and green energy. In addition, we made the verges more biodiverse and the traffic signs bio-based.
The result: a green and safe road. The bumpy, outdated road has been transformed into a smooth road that lasts for years to come.
Meer informatie?
Joep Hartjes
Managing Director Ballast Nedam Road Specialties
As Managing Director of Ballast Nedam Road Specialties, Joep is responsible for the realisation of specialist projects in the field of road infrastructure.
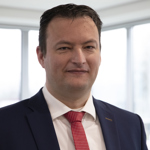