New lifting training increases safety on construction sites
In 2023, a practical lifting training course was developed in collaboration with Mammoet Academy. This course matches what employees need in practice. The enthusiasm is so great that the training is now fully booked for months in advance. This initiative dovetails seamlessly with the Take Care safety programme.
The new lifting training fits squarely within the Take Care safety programme, which was launched in 2022. A year later, the number of accidents within Ballast Nedam had roughly been cut in half. What is the secret behind this success? “The connection cannot be pinpointed exactly”, nuances Geert van der Linde, Director of Health, Safety & Environment (HSE). "But I am convinced that Take Care is having a very positive impact. This is due to a clear shift in our approach. Previously, we mainly based safety on technology and rules. But with Take Care, we put people at the centre. The focus is on attitude and behaviour. As a result, safety is no longer a subject for the HSE department. Safety belongs to everyone. Everyone is responsible for their own safety and that of their colleagues."
Soft skills
Within Take Care, the name of the programme says it all, we focus on genuine care for each other. It is all about so-called soft skills, such as paying attention to each other, calling each other to account if something is not going well and discussing dilemmas. How do you position these kinds of skills in the sometimes still somewhat traditional construction sector? "You do indeed have to break through a certain barrier in certain places in the organisation," says Geert. "We have a lot of technical people in-house. Traditionally, the best carpenter advanced to foreman, and the foreman became site supervisor. In such a system, problem-solving ability is rewarded, which is fine. However, there is less focus on skills in communication, motivation and giving instructions. While these are so important if you all want to work safely. But of course, we don't want to lose those good, technical people. They are of great value to the company. That is why we complement their existing qualities with soft skills. People learn how to deal with each other, how to motivate each other and how to have a good conversation. The great thing is that this also simply makes everyone work more effectively together. Safety and productivity go hand in hand. If we have fewer incidents, we can work better. So soft skills are actually not so soft, because they increase effectiveness and productivity."
Safety is about who you are
To make Take Care permeate the entire organisation, training courses have been developed together with external trainers. One of these is Brain Based Safety, which is tailored in seven variants to the construction site, among others, but especially also to work preparation. "Outside, they really do want to work safely," Geert knows. "But then you have to arrange that well in advance. You do this, for instance, by making a good layout for a building site, so that lorries carrying building materials never have to drive in reverse but can always leave the site going straight ahead. That way, you avoid a situation that involves standard risks. We sometimes say: we need to think ahead, instead of just thinking."
Another learning method is Safety Awareness Team training. Topics covered in this course include the importance of reporting unsafe situations and interrupting an activity if it is found to pose risks. Geert: "I have seen employees at those training sessions come in in the morning with an attitude of, 'I'm here just because I have to be'. But by the end of the day, they were all excited because they had learned to look at themselves differently. Logical, because safety is about each person's own attitude and behaviour. It says something about who you are. Are you taking good care of yourself and your colleagues, or not? And how does that translate to the private situation? Actually, it's just fun to work on that. It really helps you. That is what we try to convey with attractive and accessible training courses."
Tailor-made
The new lifting training course is a good example of such an attractive and easily accessible training. Safety coach Frank von Lumich, from Ballast Nedam subsidiary Laudy Bouw, was involved in its development. What prompted this? "There was already mandatory lifting training. That is fine for complex lifting activities, but actually far too heavy and extensive for the simple, everyday lifting activities. We got signals about that from the practice, and we picked up on them." Frank started talking to a trainer from Mammoet Academy, Laudy's regular lifting partner. They looked at existing training courses and tailored them by removing the elements that are not relevant to this target group. "In fact, the biggest pitfall is that you give a training course where people notice after an hour that it is not really about what they encounter at work," says Laudy. That is why this new training course, in addition to a bit of theory, consists of practising tasks that are common. Think about hoisting in a staircase or installing wide slab floors."
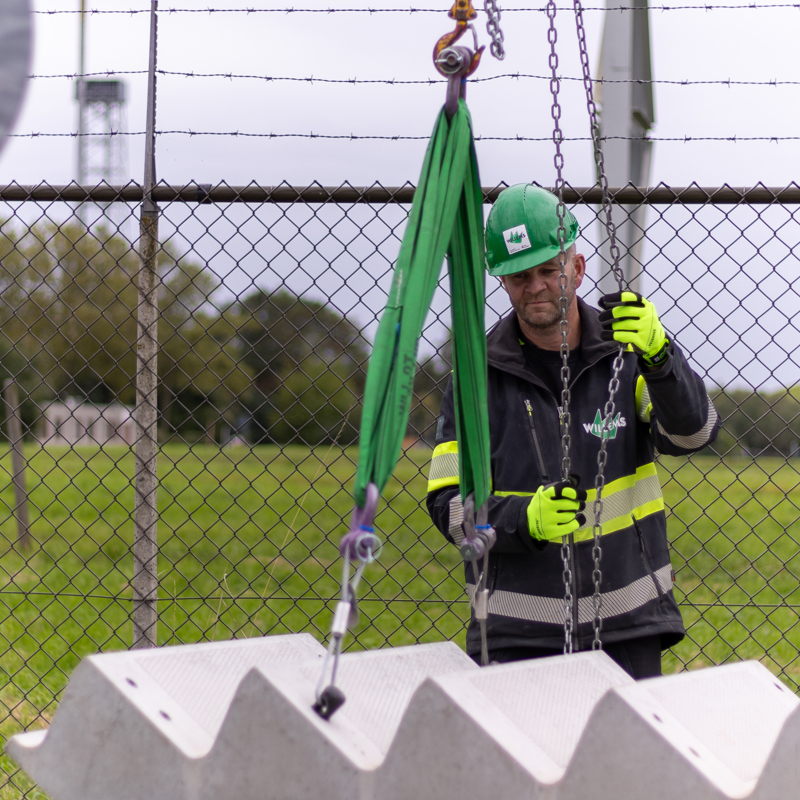
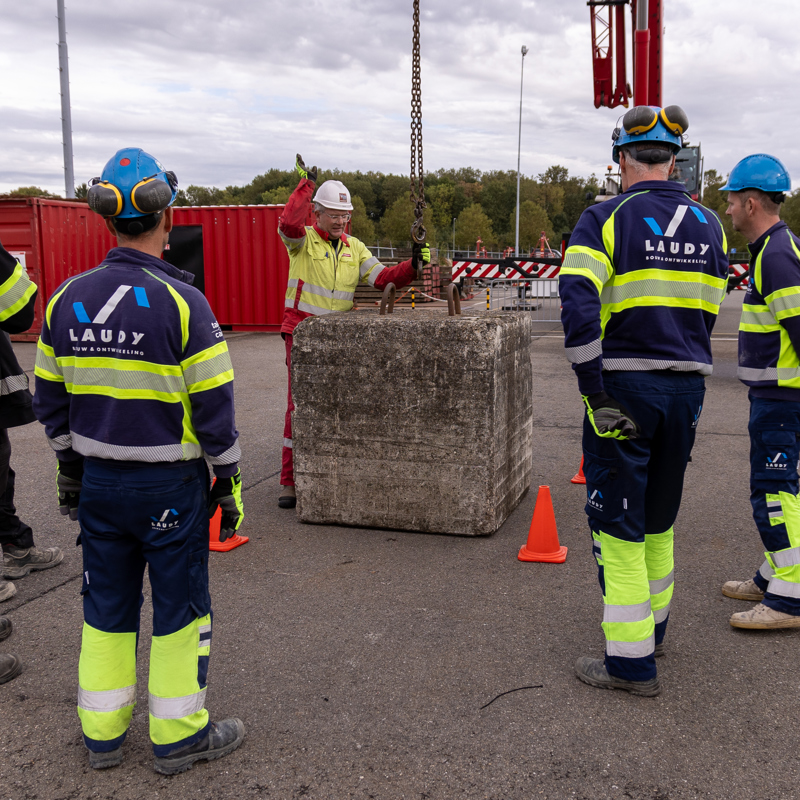
Humour
In 2023, 20 employees of Laudy Bouw and sister company Willems Bouwbedrijf attended the two-day training course in small groups of four. These included foremen, carpenters and others who perform simple lifting tasks on the construction site. One of them is Roel van den Brandt. "I probably thought too easily, but the training gave me new tools to work even more safely in practice. I learned how to correctly pick up different building materials and how they should be hooked up. And whether lifting belts are strong enough and which calculations we need to make to know how best to lift. A complete and useful course that I recommend to everyone." Frank is not surprised that the training has been received so positively. "Mammoet Academy's trainer has a lot of experience and is a crane operator himself. He knows how to keep the trainees' attention. The fact that he does this with a good dose of humour obviously helps. Beforehand, he and I toured suppliers to see if they had any spare parts for the training course. For instance, we now have pallets and wide slab floors available, which people also use on the construction site."
Fewer incidents
By 2024, all of Laudy and Willems' approximately 80 construction site employees are expected to take the new training. After successfully completing the training, participants will receive a certificate valid for five years. "In practice, this means that we will soon have at least one certified hoisting employee on every construction site," says Frank. He points out that the news of the training is spreading like wildfire. "There is a lot of interest. We are even getting requests from subcontractors and precast concrete plants."
Geert knows that the training will also be rolled out broadly internally. There is interest from Ballast Nedam West and South business units, as well as subsidiary Heddes. "The training is already fully booked for months in advance. It clearly meets a need. Dozens of serious incidents occur in lifting operations every year in the Netherlands. With this training we ensure that our professionals can perform common, simple lifting activities even more safely. The expected result: fewer lifting incidents. That's what we do it for!"