Construction of Princess Amalia Harbour quays
Commissioned by the Port of Rotterdam, and together with our trusted partners HOCHTIEF and Van Oord, Ballast Nedam is building the extension of the Prinses Amaliahaven. Rotterdam strives to remain the largest port of Europe. To achieve this, the port must be prepared to accommodate the world’s largest container ships. This project involves 2.4 kilometres of intelligent quay wall expansion.
-
2.4 kilometres of intelligent quay wall
-
1,825 metres deep-sea quays
-
360 metres earth retaining walls
2.4 kilometres of new quay wall
Every day, approximately 356 sea and inland vessels sail through the port of Rotterdam. This number is increasing – partly due to e-commerce. Also, the size of the containerships is increasing. By constructing new deep-sea and inland navigation quays in the Princess Amalia Harbour, the various container terminals will have the space they need to develop further. They will also be able to load and unload more ships with larger sizes. The new construction is planned on both sides of the port and consists of 1,825 metres of deep-sea quay, 160 metres of inland quay and 360 metres of earth retaining walls.
An innovative quay wall
Not only the scale of the quay wall makes this project special. The Princess Amalia Harbour project also distinguishes itself from other projects in terms of technology. The quay wall is going to be ‘smart’ and is equipped with all kinds of sensors that monitor forces and deformations. This enables technicians to monitor movements of the quay wall when ships dock for example. Our client Port of Rotterdam can use this information for follow-up projects and for the maintenance of the quays. Moreover, thanks to smart sensors, fewer physical inspections are needed.

Less nuisance, less emissions
In line with the Rotterdam mentality, we work practically and effectively. On top of that, we work in a sustainable way. We minimise disruption to the surrounding area by transporting construction materials, such as steel and piles, by water. This causes less disruption on the roads and less construction traffic, while the processes of the container terminals can proceed. Our machines run on Hydrotreated Vegetable Oil (HVO) which reduces CO2 emissions by 90% compared to regular diesel. We mainly work with electric cranes and use ‘green’ electricity. This way, we share a responsibility to reduce harmful emissions, in line with our client’s ambitions,. Last but not least: we install ECOncrete blocks at two locations. These serve as artificial reefs to stimulate underwater biodiversity.
Working safely together
During a large-scale project like the Princess Amalia Harbour – where many logistic routes come together and that is also located near water – safety is given extra importance. As early as the tendering phase, we developed a conceptual plan to separate the transport routes via land and water. Also, at specific times of the day, no materials will be delivered to the project. This way, we guarantee traffic safety, both on land and water. For example, there are separate access roads for pedestrians and construction traffic, there is a separate walkway along the construction road, the construction roads are designed carefully and we use traffic rules for construction traffic. In addition, we use performance indicators to manage neat and orderly work sites. This ensures a safe working environment at a place where we work on our joint future.
More information?
Sander Lefevre
Managing Director Ballast Nedam Infra Projects a.i.
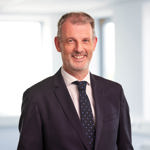