Modular construction
One of our expertise
Ballast Nedam deploys a lot of expertise daily, modular construction included. We carry out this expertise from Ursem Modulaire Bouwsystemen (UMBS), which has grown into one of the most advanced modular system suppliers in Europe. Ursem Modulaire Bouwsystemen works closely together with our organisational unit Heddes Bouw & Ontwikkeling.
This is how we build modularly
Once the design has been approved, a prototype can be built. This prototype is tested and approved by our client before proceeding to the production of the series. The modules produced, including the installations, façades and interiors, are tested on the production line before release. This allows us to guarantee a perfect product upon delivery.
When the modules arrive at the construction site, they are put in place by a crane, after which they are linked. The installations for water, sewerage, air and electricity are connected to the central pipes. The façade is are further finished, resulting in a seamless, high-end building.
The tallest modular project in the Netherlands
On the 'Laan van Spartaan' in Amsterdam, Ursem Modulair Bouwen and Heddes Bouw & Ontwikkeling built a unique modular building of sixteen floors, the tallest modular project in the Netherlands. In just fourteen months, we built the 361 student residences. This was only possible because the houses were fully produced at the factory.
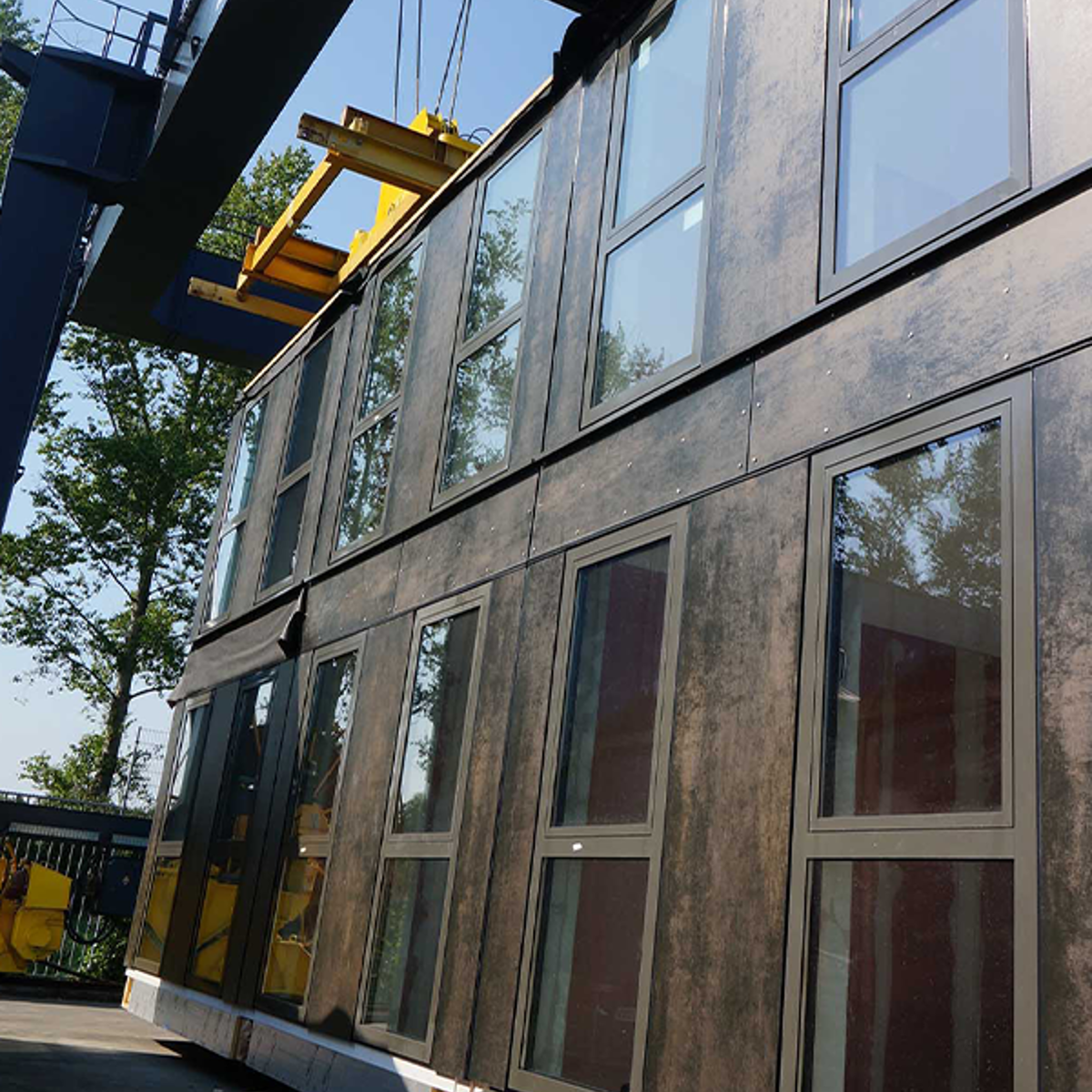
From BIM to finishing-touch
The process is as follows: all elements are set up in BIM and designed digitally. This digital information is sent to the machinery for sawing the wooden parts and plates. The timber frame construction elements are produced fully automatically with CNC milling machines. In the second part of the factory, the module is assembled on the conveyor belt, starting with the concrete floor to which the supporting structure, walls and roof are mounted. After which, the finishing and installation are done. The residential modules are completely windproof and waterproof and are finished for transport.
Residential housing is composed of multiple modules up to 4 meters wide. Linking modules on location ensures that we can produce a vast number of housing types.
The advantages of modular construction
Modular construction projects are also less vulnerable to weather conditions and are not dependent on many subcontractors. In the factory, the production processes are energy efficient, and the waste production is less than 1%, while in traditional construction, it is 10-15%. Modular construction leads to fewer transport movements, which results in a reduction of noise, nitrogen, dust, traffic jams and CO2 emissions. Once arrived on site, the modules are already equipped with installations and interiors.
Modular construction also offers many advantages at the level of sustainability and circularity. For example, by building modularly, it is easier to achieve high BREEAM or LEED scores. Most modules can also be disassembled so that our client can respond to a continuously changing market, and the modules and elements can be reused for a sustainable future.
Discover more: PuurThuys, our concept homes
With PuurThuys we build from a concept in which the construction process is standardised. We make it extra easy for our customers. In four steps, we realise homes that are perfectly tailored to the target group. Because the construction method and techniques are already known in advance, we can build quickly and predictably. After all, we know exactly where we stand.
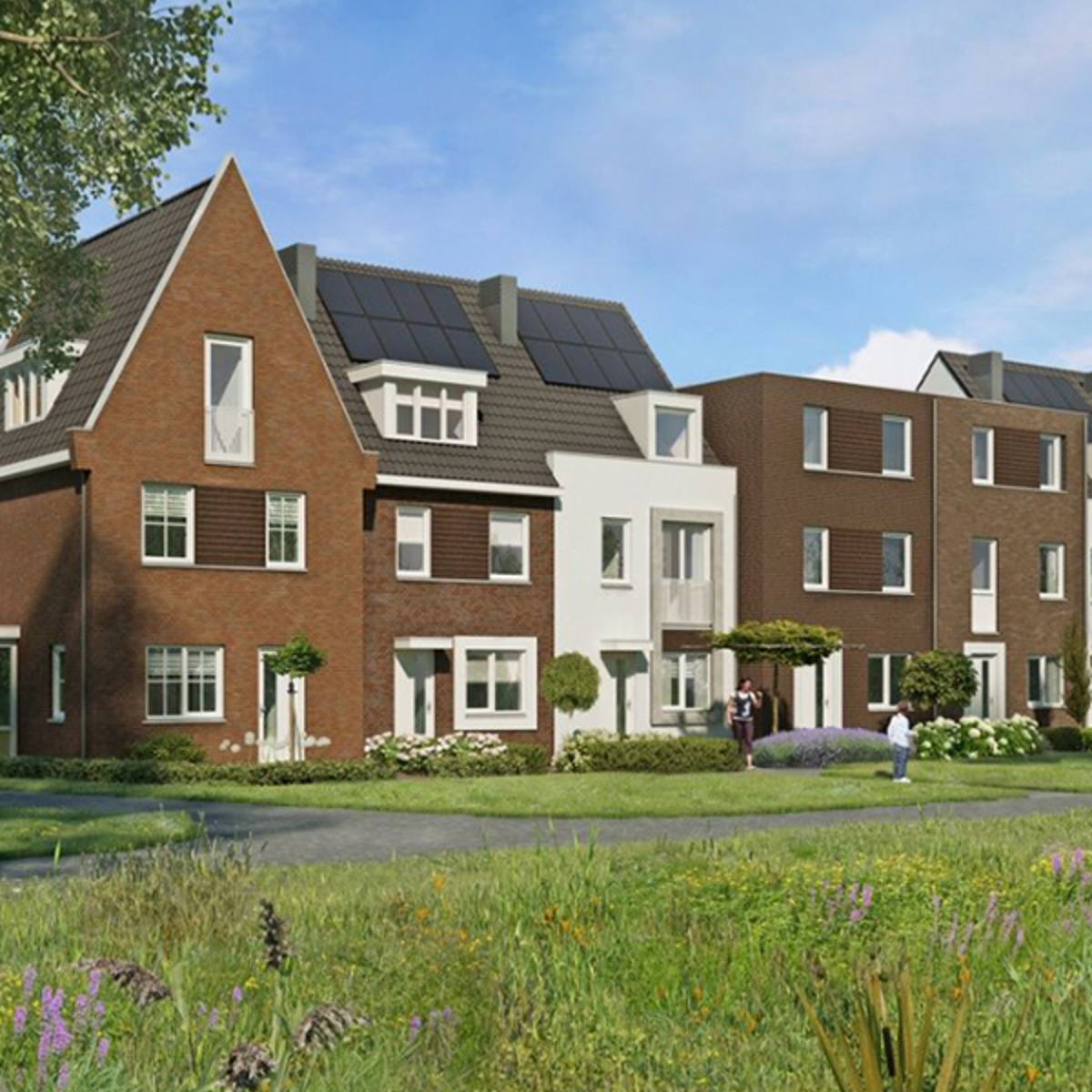
-
Heddes Bouw & Ontwikkeling
- Keern 31, Hoorn
- Tel: +31 (0)229 282 400