Tunnels
One of our expertise
Ballast Nedam deploys a lot of expertise daily, tunnel construction included. Tunnels are indispensable in our infrastructure. The Netherlands alone has many tunnelled waterway crossings so that traffic and shipping can continue undisturbed. Various types of tunnels have been built in the Netherlands, of which the immersed tunnel is the most prominent.
Ballast Nedam has built up years of experience by working on many tunnelling projects. The A24 Blankenburgverbinding in the busy port area of Rotterdam and the A9 Gaasperdammertunnel, the longest land tunnel in the Netherlands in Amsterdam, both DBFM projects, are the most recent examples. Through this knowledge and experience, we can realise every type of tunnel from start to finish. We have the knowledge and specialists in-house to analyse individual situations accurately and implement the most suitable tunnel solution to the millimetre.
Which tunnels do we realise?
1. Cut-and-cover and land tunnels
Cut-and-cover tunnels are a traditional method of tunnel construction mainly used in urban areas. Due to the soft soil combined with groundwater in the Netherlands, sheet piling or diaphragm walls are often required first, creating a construction pit. The ground is then excavated, which often requires heavy stamps between the sheet piling to prevent deformation and the risk of subsidence in the surrounding area. An underwater concrete floor anchored with anchor piles is installed, after which the construction pit can be dried. We eventually realise the tunnel within the dry construction pit. The Holland Tunnel, part of the Blankenburg connection, is a good example of a cut-and-cover tunnel.
For inland tunnels, we can often avoid going deep underground, which allows us to keep clear of groundwater. The tunnel is then built from ground level, as it were.
2. Tunnel boring machine technology (TBM)
TBM construction has the great advantage of moving under the ground like a mole with great precision without causing major inconvenience above-ground. This is very practical in inner-city spaces, for example. This tunnelling method is also used for the passage of rocky mountain massifs. Using this method, we drill through rock, soft soil and sandy soil. We are proud of the Gotthard Base Tunnel through the Alps in Switzerland, which our organisation unit Heitkamp Construction Swiss completed in 2016. With two single tunnel tubes of 57.09 kilometres, the tunnel is the longest rail tunnel in the world. The Heitkamp Construction Swiss team is specialised in this field and is independently capable of constructing TBM tunnels.
3. Immersed tunnels
Immersed tunnels are often used at waterway junctions. We build concrete tunnel elements in a construction dock. The elements are temporarily closed on both sides with bulkheads, floated and transported to the immersion location. At the immersion location, a trench is dredged in the riverbed. The tunnel elements are immersed one by one in a controlled manner. This is precision work that needs to be done very carefully. Once immersed and in place, rubber GINA gaskets form the watertight connection between the tunnel elements and the temporary bulkheads are removed. This tunnelling method is used for the Maasdelta tunnel within the A24 Blankenburgverbinding, crossing the Nieuwe Waterweg in Rotterdam.
Safety #1
Because the safety of road users is the highest priority, a standard safety level for tunnels has been devised in collaboration with Rijkswaterstaat and several construction and installation parties. If a vehicle comes to a standstill, it is immediately signalled by the tunnel’s technical installations. When the cameras detect the vehicle, the system acts immediately and determines, based on analyses, whether or not to implement speed-limiting measures or even close the tunnel.
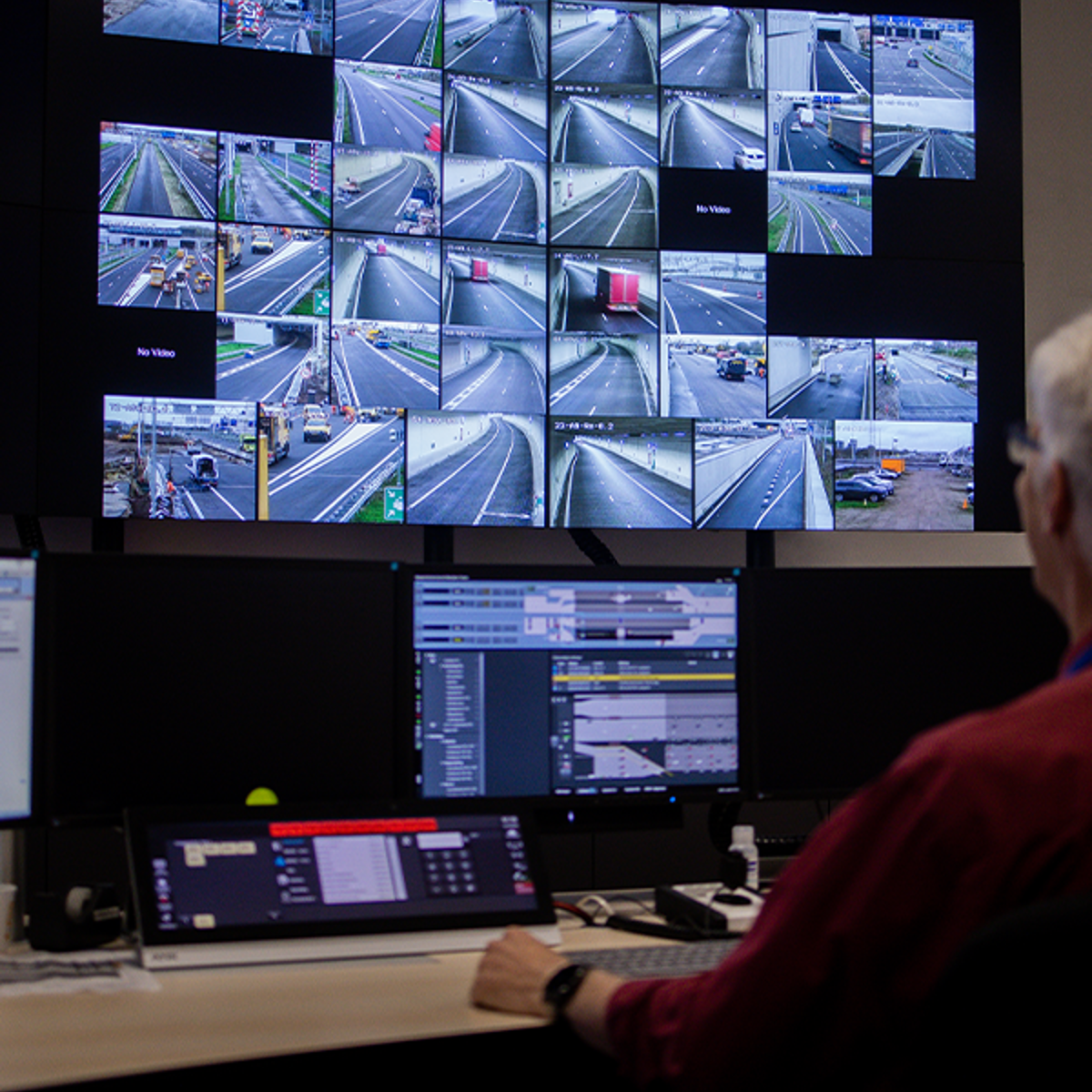
Our people are our strength
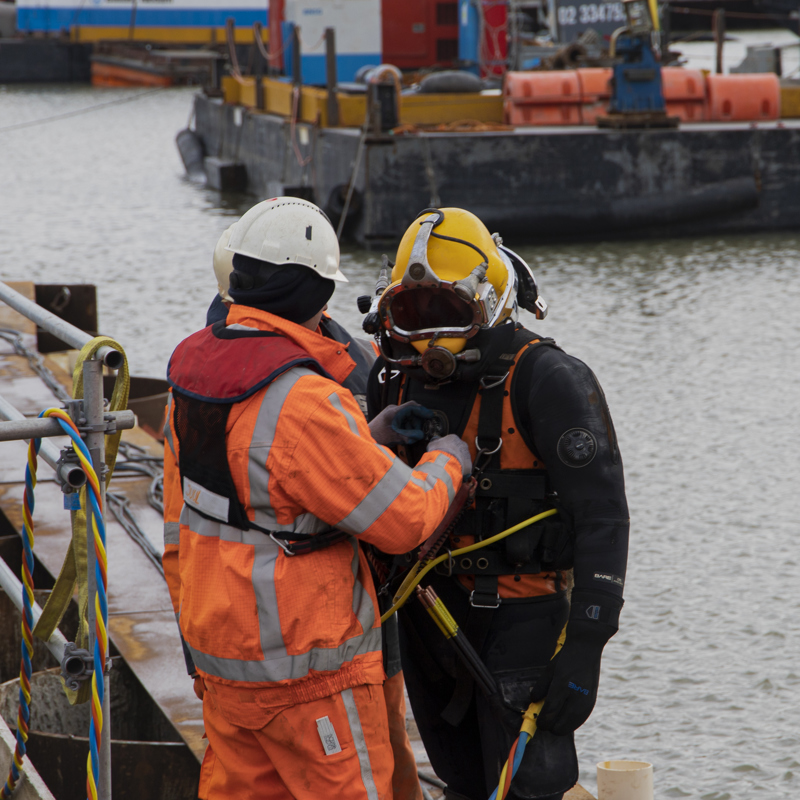
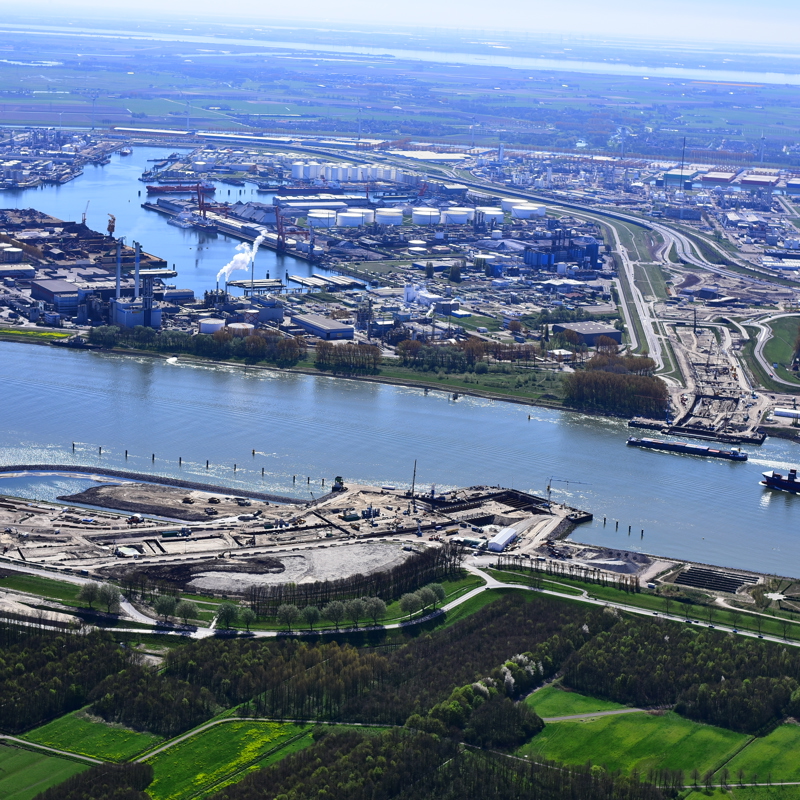
“The salinity of the water has an enormous influence,” Martijn explains. “Freshwater has a density of 1000 kilograms per cubic meter of water, making a thousand litres of freshwater weigh exactly one thousand kilograms. But saltwater is heavier and varies between 1021 and a maximum of 1027,5 kilograms per cubic meter. If a floating tunnel element protrudes about 20 centimetres above water during transport in freshwater, then that is about double in saltwater. I can still remember the tunnel elements of the Burgemeester Thomassen tunnel, built in a freshwater area, slowly emerging from the water on their way out at sea. In such a case, to get the tunnel element down again, we have to add the same amount of extra volumetric weight of water in ballast tanks. When the tunnel element is in place, the ballast water in the ballast tanks is replaced by a layer of ballast concrete on the floor of the tunnel and soil on the roof.”
Smart logistics
This smart construction ensured that we won the project and then successfully executed it. Traffic could continue on its way while we broke Dutch records with the scope of this project. The collaboration with the client, Rijkswaterstaat, resulted in the timely and error-free commissioning of the tunnel.